Investment Casting
The investment casting process involves making a wax duplicate of the casting by injecting wax into an aluminum mold. Several copies of the wax part are then assembled onto a sprue to create a “tree”. The wax tree is then dipped into a ceramic slurry several times to create an outer shell coating. Next, the shell is placed in an oven to melt and drain out the wax, thus creating cavities ready to receive molten metal. The metal is poured into the shells creating the castings. Once the metal has cooled, the shell is knocked off leaving a “tree” consisting of the castings, ingates and sprue. In the finishing department, the castings are cut off the tree, and finished by grinding or sanding any remnants of the ingates.
Advantages
Excellent surface finish, very smooth (about 125 microinches or 3.2 micrometers). |
Easier to design because no draft angle is required. |
Hold tighter tolerances such as +-0.010”(0.25mm). |
Used for casting any metal, ferrous or nonferrous. |
Both 3D printed wax and plastic patterns may be used. |
Molds are machined from aluminum (for excellent heat transfer) and do not wear. |
Design Considerations
No draft angle required. |
Apply generous radii or fillets on all inside and outside corners. This helps with metal flow, reduces “hot tearing” as the metal cools, and improves strength and attractiveness of castings. |
Consistent and even wall section thickness is best. Shrinkage porosity develops in thick section areas. |
General tolerance of +-0.010”(0.25mm) up to 6”(152mm). |
Sand Molding
The No-Bake Sand casting process involves creating a mold using sand and resin. Sand is packed around a pattern that contains the imprint of the casting to create a cope (top half of sand mold) and drag (bottom half of sand mold). Molten metal is poured into the sand mold, through the runner and gating system and allowed to cool and solidify. The sand is broken away from the metal and recycled to create more molds. The metal casting is finished by cutting and grinding any excess metal. Further processing may include heat treating, machining or painting.
Advantages
May be lower cost than other casting processes. |
Fast way to cast near net shape parts. |
Patterns may be made of a variety of materials including wood, plastic, and aluminum. Sometimes steel, styrofoam, 3D plastic prints or existing castings are also used as patterns. |
Used for casting any metal, ferrous or nonferrous. |
Design Considerations
3 degrees of draft angle is required from the parting line. |
Apply generous radii or fillets on all inside and outside corners. This helps with metal flow, reduces “hot tearing” as the metal cools, and improves strength and attractiveness of castings. |
Consistent and even wall section thickness is best. Shrinkage porosity develops in thick section areas. |
General tolerance of +-0.040”(1.02mm) per 12” (305mm). |
Heat Treating
Stress Relief • Anneal • Normalize
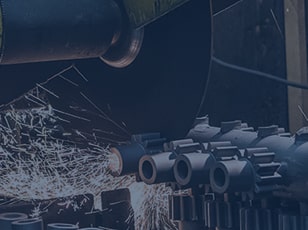
Our Products
We will work with you to determine product goals and design specifications to ensure ideal performance and value, all while accounting for costs.
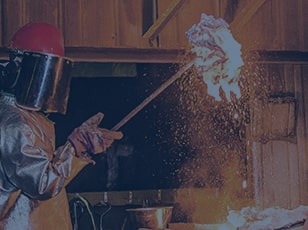
Manufacturing Process
We take care of all
manufacturing logistics.
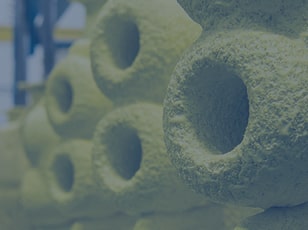
Technical Specifications
We will work with you to test initial product samples to ensure satisfaction.
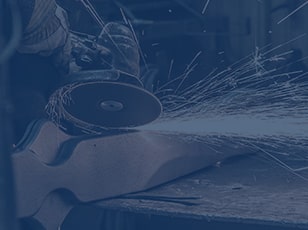
Certifications
We establish on-site quality assurance standards and procedures to ensure your specifications are met.
Contact us for a quote today!